Commercial and industrial environment settings require pressure switches that are not only durable but also precise and capable of adapting to the demanding conditions inherent in larger systems. Unlike residential water systems, commercial and industrial applications often involve greater complexity and require more robust solutions to handle the heavy-duty demands of water distribution, manufacturing processes, and fire suppression systems.
A. Key Applications of Pressure Switches in Commercial and Industrial Settings:
One of the most critical roles of these switches is to maintain a consistent water pressure in systems that serve multi-story buildings, hospitals, hotels, and large office complexes. In these settings, water demand can fluctuate significantly, especially during peak usage hours. To address these fluctuations, water pressure switches in such systems must have a wide adjustable pressure range—typically between 50 and 150 psi—and must respond quickly to changes in pressure. Heavy-duty electronic pressure switches, which feature programmable settings for precise control, are typically recommended for such applications. These switches allow for accurate adjustments and are designed to cope with the high demand of these complex systems.
– Manufacturing and Process Industries
Another significant application of water pressure switches in commercial and industrial environments is in manufacturing and process industries. These industries require regulated water pressure for cooling systems, boilers, and chemical processing, all of which are essential to their operations. The water pressure switches used in these systems must be resistant to extreme temperatures, vibrations, and exposure to corrosive fluids. For this reason, pressure switches made of stainless steel or coated with epoxy are ideal for such environments. Additionally, these switches must be equipped with chemical-resistant diaphragms to ensure longevity and reliable performance in harsh conditions.
– Fire Suppression Systems
Water pressure switches are also critical in fire suppression systems, where they help maintain the required pressure for sprinkler systems during emergencies. These systems must operate flawlessly under high-stress conditions to comply with National Fire Protection Association (NFPA) standards. Given the importance of these systems, pressure switches for fire suppression must be fail-safe and highly reliable. For optimal performance, pressure switches in fire suppression systems are often UL-listed and come with battery backups to ensure they work when needed most.
– Agriculture and Irrigation
In agriculture, particularly in large-scale irrigation and farming operations, water pressure switches play a role in automating water flow. These systems can face challenges such as dust, moisture, and voltage fluctuations, especially in remote locations. For these applications, pressure switches that are weatherproof, able to handle wide voltage ranges (typically between 100V and 480V), and equipped with surge protection are essential. This ensures that the irrigation systems function smoothly without interruptions, regardless of the environmental conditions.
B. How to Select the Right Pressure Switch for Commercial and Industrial Applications:
– Pressure Range and Accuracy
Selecting the right pressure switch begins with understanding the system’s pressure requirements. While residential systems typically operate in the range of 30 to 50 psi, commercial and industrial systems may need pressure switches that can handle up to 200 psi. Precision is crucial for these larger systems, and electronic pressure switches offer far better accuracy than mechanical ones—±1% as opposed to ±5%.
– Durability and Material Considerations
Durability is another critical factor. In industrial settings, the pressure switch must be able to withstand harsh environmental conditions. Stainless steel or brass housing materials are often preferred for their corrosion resistance, while diaphragms made of EPDM or Teflon are essential for chemical and abrasion resistance. These materials ensure the longevity and reliable operation of the switch.
– Electrical Compatibility
Electrical compatibility is vital when choosing a pressure switch. The switch must be able to handle the correct voltage, current, and phase requirements, which vary based on the pump system in use. For example, a 10 HP pump will require a switch that is rated for over 30 amps. Verifying these specifications ensures the switch can operate efficiently with the pump and prevent electrical issues.
– Environmental Factors
Another consideration is the environmental conditions in which the switch will operate. A high Ingress Protection (IP) rating is essential to ensure that the switch is protected from dust and water. An IP rating of 65 or higher is usually recommended for industrial use. Additionally, the temperature range in which the switch can operate is critical for systems exposed to extreme temperatures. Choosing switches that can operate within a temperature range of -40°F to 200°F ensures reliable performance in all conditions.
– Certifications and Compliance
Water pressure switches used in commercial and industrial settings must also comply with industry standards and certifications for safety. Look for switches that are UL-listed, CE-certified, or NSF-compliant to ensure that they meet regulatory standards for safety and performance.
C. Common Challenges and Solutions in Commercial and Industrial Water Pressure Switch Systems:
Despite their reliability, water pressure switches can experience problems in industrial settings. Common issues include frequent cycling of the pump, pressure drops, and electrical failures. These problems are often caused by factors such as waterlogged tanks, pipe leaks, or burnt contacts. Regular inspections, such as checking for leaks, corrosion, and unusual noises, can help identify potential issues early. Annual calibration of the switch and its settings is also crucial for maintaining accurate performance. Replacing the switches every 5 to 7 years is generally recommended, as industrial environments can cause them to wear out faster due to the heavy usage they undergo.
D. Maintenance Best Practices for Water Pressure Switches:
– Regular Inspections and Calibration
To ensure that water pressure switches continue to perform efficiently, regular inspections and calibration are necessary. Monthly checks for leaks, corrosion, and any unusual noises can help identify minor issues before they become significant problems. Additionally, annual calibration to test and adjust the cut-in and cut-out pressures is important for maintaining accuracy and system reliability.
– Switch Replacement
Water pressure switches in commercial and industrial applications typically experience more wear and tear than residential models due to heavy usage. It is recommended to replace them every 5 to 7 years to prevent breakdowns and avoid unexpected system failures.
Conclusion
In conclusion, water pressure switches are essential for ensuring the efficient and reliable operation of water systems in commercial and industrial environments. By choosing the right switch for each application—based on pressure range, durability, and environmental factors—and following proper maintenance practices, businesses can prevent system failures, minimize downtime, and avoid costly repairs.
Reps Global Group LLC. Content Team
Keywords: water pressure switches, commercial, industrial, water systems, large-scale, distribution, manufacturing, fire suppression, cooling systems, pressure range, accuracy, durability, material, stainless steel, brass, diaphragm, electrical compatibility, environmental factors, ip rating, temperature range, certifications, compliance, challenges, maintenance, inspections, calibration, leaks, corrosion, replacement.
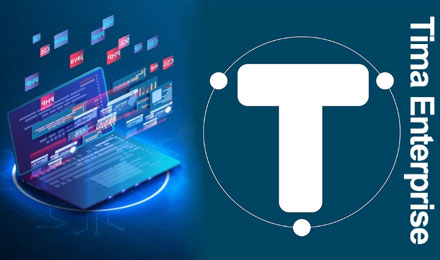
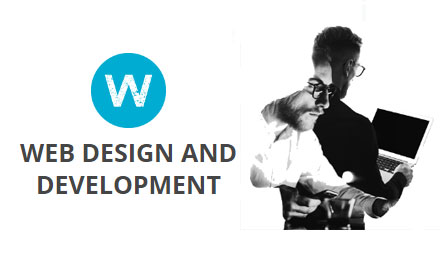